در این بخش از سری مطالب «هیدرولیک و فیلتراسیون» به آسیبها و هزینههای ناشی از آلایندهها در سیستمهای هیدرولیک خواهیم پرداخت. این سری مطالب در ده بخش و با هدف کمک به نشر آگاهی عمومی در زمینه فیلتراسیون سیستمهای هیدرولیک منتشر میشود.
آسیبهای ناشی از آلایندهها در سیستمهای هیدرولیک
حدود ۹۵ درصد از تمام مشکلات سیستمهای هیدرولیک ناشی از گرما، فرآیند مونتاژ سیستم و ورود آلایندهها به سیستم است. مشکلات ناشی از گرما معمولاً مربوط به طراحی و متریال مورد استفاده در ساخت سیستم هستند و مشکلات بهوجود آمده در روند مونتاژ اکثراً به اتصالات و نحوه نصب آنها برمیگردد. در این میان، مشکلات مربوط به آلایندهها بیشترین مشغولیت ما در فیلتراسیون را به خود اختصاص میدهد، زیرا تجربیات طراحان و کاربران سیستمهای هیدرولیک نشان میدهد که ۷۵ درصد تمام مشکلات این سیستمها بطور مستقیم ناشی از آلایندهها است.
آلایندهها میتوانند به واسطه ایجاد اختلالهای جدی در عملکرد روغن هیدرولیک، هزینههای سنگینی را به سیستم تحمیل کنند. چهار عملکرد اصلی روغن هیدرولیک به این شرح است:
- عمل به عنوان محیط انتقال انرژی
- روانکاری اجزای متحرک داخلی
- عمل به عنوان محیط انتقال گرما
- درزبندی اجزای متحرک
درصورت بروز اختلال در هریک از این عملکردها، سیستم هیدرولیک به روش مورد انتظار در طراحی عمل نخواهد کرد. توقف تولید احتمالی ناشی از این اختلالات میتواند در هر ساعت چندین هزار یورو هزینه را به یک کارخانه بزرگ تحمیل کند، که با نگهداری و استفاده مناسب از روغن هیدرولیک میتوان دفعات توقف پیشبینینشده را کاهش داده و از این هزینهها اجتناب کرد. مشکلات به وجود آمده بر اثر ورود آلایندهها به سیستم میتواند هزینه های مختلفی را به سیستم تحمیل کند:
- توقف تولید
- هزینههای جایگزین کردن اجزا و قطعات
- تعویض مداوم سیال
- انهدام پرهزینه روغن
- افزایش کلی هزینههای نگهداری
- افزایش میزان ضایعات
آسیبهای ناشی از آلایندهها معمولاً به شکلهای زیر اتفاق میافتند:
- گرفتگی روزنهها
- استهلاک اجزا
- تشکیل زنگ یا سایر انواع اکسیداسیون
- تشکیل مواد شیمیایی مرکب
- تغییر خاصیت افزودنیها
- رشد باکتریها
روغن هیدرولیک باید با ایجاد یک لایه روانکننده، فاصلههای میان اجزای متحرک را حفظ کند. در بهترین حالت، این لایه باید به اندازه کافی ضخیم باشد تا بتواند لقی مجاز بین این اجزا را پر کند. در چنین حالتی، استهلاک سیستم در حد پایینی باقی می ماند و به این ترتیب احتمال اینکه اجزا تا پایان عمر مفید خود (که ممکن است چند میلیون چرخه کاری باشد) قابلاستفاده باشند، افزایش پیدا خواهد کرد.
لقی مجاز در سیستمهای هیدرولیک، به بازه فاصلهای میان اجزای متحرک یا ثابت این سیستمها گفته میشود. این مقدار در مراجع مختلف به فراخور کارایی سیستم و اهمیت قطعه، اعلام شدهاست.
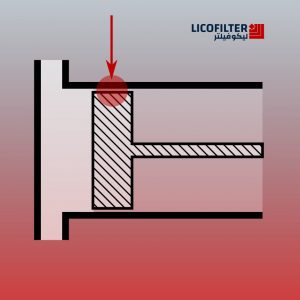
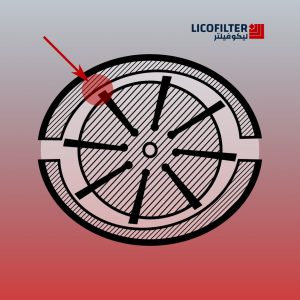
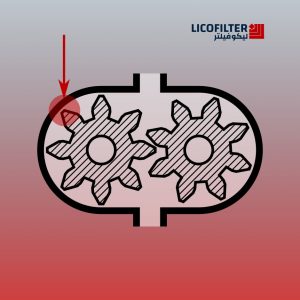
مقادیر معمول لقی مجاز برای اجزای سیستمهای هیدرولیک در جدول زیر ذکر شدهاند:
میزان لقی مجاز برای اجزای سیستمهای هیدرولیک
اجزای سیستم | لقی مجاز (میکرون) |
---|---|
یاتاقان لغزشی | 0.5 |
پمپ روتوری (پرهای) (از دورترین نقطه پره تا دیواره داخلی) |
0.5-1 |
پمپ دندهای (از چرخدنده تا دیواره جانبی) |
0.5-5 |
شیر سروو (از اسپول تا بدنه) |
1-4 |
یاتاقان هیدرواستاتیک | 1-25 |
پمپ پیستونی (از پیستون تا دیواره داخلی سیلندر) |
5-40 |
دیواره فلپر شیر سروو | 18-63 |
عملگر (اکچویتور) هیدرولیکی | 50-250 |
روزنه خروجی شیر سروو | 130-450 |
روانکاری با ایجاد لایهای از مایع روانکار در بین قطعات متحرک در فاصله لقی مجاز صورت میگیرد. ضخامت این لایه بستگی به فاصله درنظر گرفته شده در طراحی، میزان بار وارد شده بر قطعه، سرعت حرکت قطعات و ویسکوزیته مایع روانکار دارد.
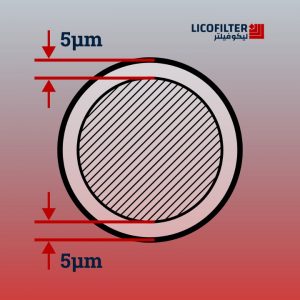
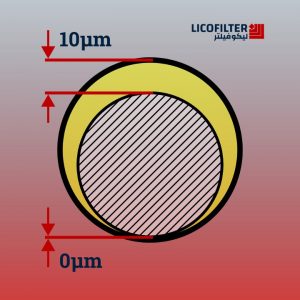
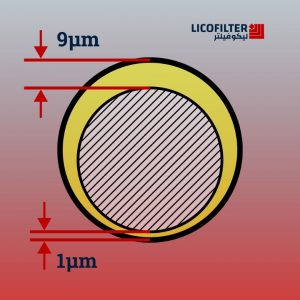
با مقایسه مقادیر لقی مجاز با سایز نسبی ذرات که در جدول زیر نشان داده شدهاست، میتوان به میزان حساسیت هریک از اجزای سیستم هیدرولیکی نسبت به اندازه آلایندههای پی برد.
سایز نسبی ذرات
ذره یا محدوده بزرگی | سایز (میکرون) | سایز (اینچ) |
---|---|---|
دانه نمک خوراکی | 100 | 0.0039 |
موی انسان | 70 | 0.0027 |
حد پایین بینایی انسان | 40 | 0.0016 |
آرد آسیابشده | 25 | 0.001 |
گلبول قرمز خون | 8 | 0.0003 |
باکتری | 2 | 0.0001 |
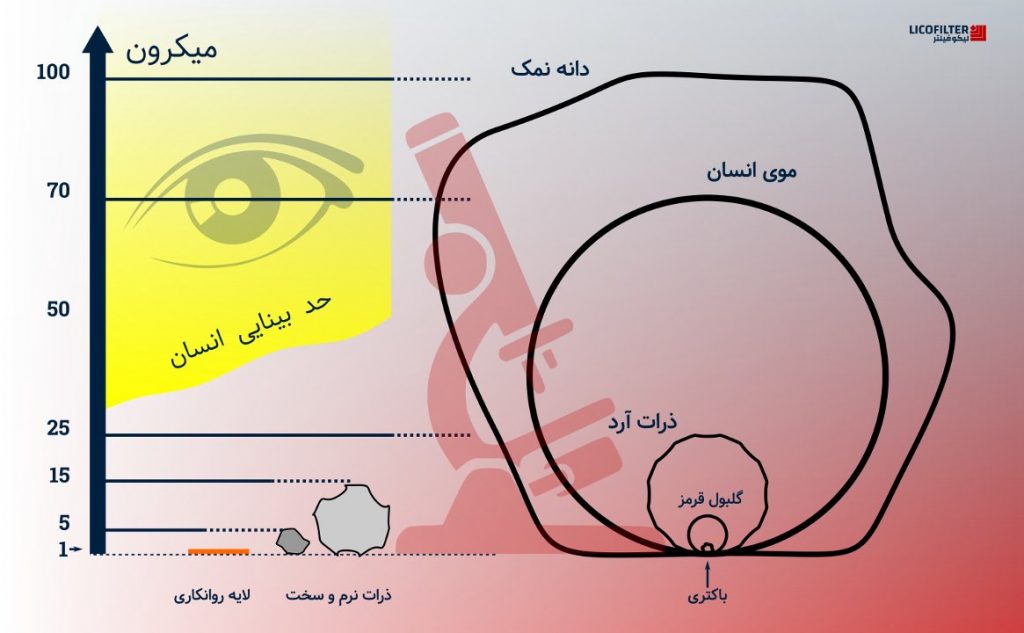